OVERVIEW
The air compressor adopts the newly developed rotor tooth profile for main structure of the diesel engine. Each type of head adopts solid axial bearing and radial bearing, so offering superior performance and longer service life.
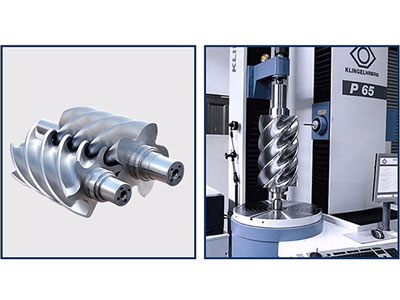
Triple shaft seal is applied in key parts to eliminate leakage problems. Wear resistant bushing and O-ring are precisely ground for high maintainability. Each product features superior performance and efficiency, providing large exhaust capacity with small motor horsepower. Oil cooler is designed according to the actual working conditions in China, with a large cooler and fan, so that it is suitable for working in harsh environment.
The air flow control system can automatically and continuously adjust the air inlet volume and rotary speed of the engine, so that the air supply and consumption are fully matched. This achieves better performance while reducing the oil consumption.
The air compressor is equipped with engines from Cummins, Yuchai and other famous brands. These engines have powerful movements, reliable operation, fuel economy and low noise, and the exhaust can reach very high environmental protection standard.
The equipped multi-stage air filter system effectively reduces the influence of harsh dusty environment on the engine. The precision filter layer of the main air filter filters out residual dust to protect the machine from wearing out. The safety filter element allows the air filter to be maintained without downtime to ensure safe operation.
ADVANTAGES
- Easy to operate
Allowing 24h unmanned operation. If no air is consumed, the compressor will stop automatically after long-time idling. When air is consumed, the compressor then starts automatically.
- Wide adaptability
The air compressor is widely applied for the coating of precision electronic parts and micro-processing industries.
- Intelligent design
The air compressor has a perfect interface control system, cooling system and inlet air filter system.
- Outstanding stability
The exhaust volume and temperature are stable after long-term operation, with no crash and low fault.
WORKING PRINCIPLE
The working principle of an air compressor can be divided into three main parts: the intake process, compression process, and exhaust process.
Intake Process: The first step in the working principle of an air compressor is the intake process. As the rotor moves, the teeth of the male rotor continuously disengage from the teeth of the female rotor. During this time, the volume between the teeth (tooth space) continuously expands and remains connected to the intake port. As the rotor rotates, the tooth space reaches its maximum volume, and at this point, it disconnects from the intake port, marking the end of the intake process.
Compression Process: With the rotation of the rotor, the volume occupied by the air trapped in the tooth space decreases, leading to an increase in gas pressure. This reduction in volume and the corresponding increase in pressure constitute the second stage of the air compressor's working principle, the compression process.
Exhaust Process: Once the tooth space connects with the exhaust port, the exhaust process begins. This process continues until the profiles at the end of the teeth fully mesh, allowing all the gas within the tooth space to be completely expelled through the exhaust port. The volume of the sealed tooth space becomes zero, indicating the completion of the exhaust process.
These three processes, when repeated continuously, allow the air compressor to intake, compress, and exhaust air to produce high-pressure gas for various applications, such as providing power and driving mechanical equipment.