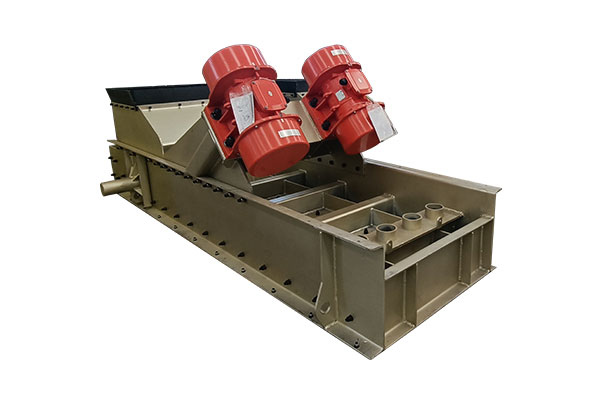
Silver crushing & processing
Silver is commonly extracted from ore by smelting or chemical leaching. Silver mining is the resource extraction of silver by mining. Silver ore beneficiation first choice is large capacity magnetic separation, followed by is electrostatic separation, and then re-election, and the minimum is flotation.
Silver involved in mixing silver ore, salt, copper sulphide, and water. A method called the cyanide, or heap leach, this process has gained acceptance within the mining industry because it is a low-cost way of processing lower-grade silver ores.
1. Silver ore is crushed into pieces, usually with 1-1.5 in (2.5-3.75 cm) diameters, to make the material porous. Approximately 3-5 lb (1.4-2.3 kg) of lime per ton of silver ore is added to create an alkaline environment.
2. Broken or crushed (by jaw crusher, cone crusher or impact crusher, and ball mill) silver ore is stacked on impermeable pads to eliminate the loss of the silver cyanide solution. Pad material may be asphalt, plastic, rubber sheeting, and/or clays. These pads are sloped in two directions to facilitate drainage and the collection of the solutions.
3. A solution of water and sodium cyanide is added to the silver ore. Solutions are delivered to the heaps by sprinkler systems or methods of ponding, including ditches, injection, or seepage from capillaries.
4. Silver is recovered from heap leach solutions in one of several ways. Most common is Merrill-Crowe precipitation, which uses fine zinc dust to precipitate the precious metal from the solution. The silver precipitate is then filtered off, melted, and made into bullion bars.
5. Other methods of recovery are activated carbon absorption, where solutions are pumped through tanks or towers containing activated carbon, and the addition of a sodium sulfide solution, which forms a silver precipitate.