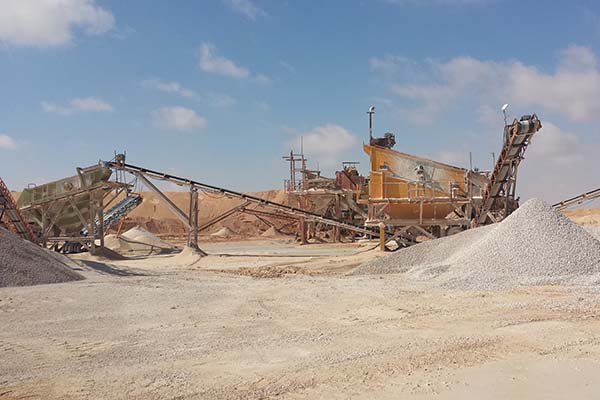
Limestone Crushing&Screening Plant in Saudi Arabia
- Type: Semi-Mobile(mounted on steel structure)
- Max Feeding Size: 500mm
- Final Output Size: 0-3mm, 0-3/16”, 3/16”-3/8”, 3/8”-3/4”
- Capacity: 100TPH
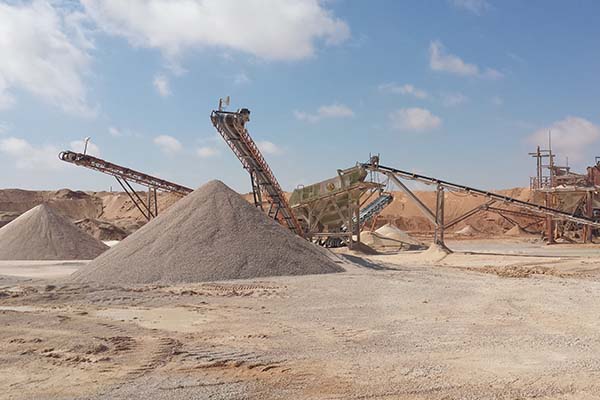
On September 13 of 2010, one customer from No.1 Engineering Company in Riyadh, KSA ordered a complete set of limestone crushing and screening plant, including:
-
1.Hopper: LC3000x3000
-
2.Grizzly Vibrating Feeder: GZD960x3800/1 set
-
3.Primary Jaw Crusher: PE600x900/1 set
-
4.Secondary Impact Crusher: PF1214/1 set
-
5.Vibrating Screen: 2YZS1237/1 set
-
6.Vibrating Screen: 3YZS1848/2 sets
-
7.Belt Conveyor: 12sets
-
8.Dust Collector
-
9.Steel Structure
We loaded and shipped these goods in 10x40'HQ from Qingdao to Dammam port.
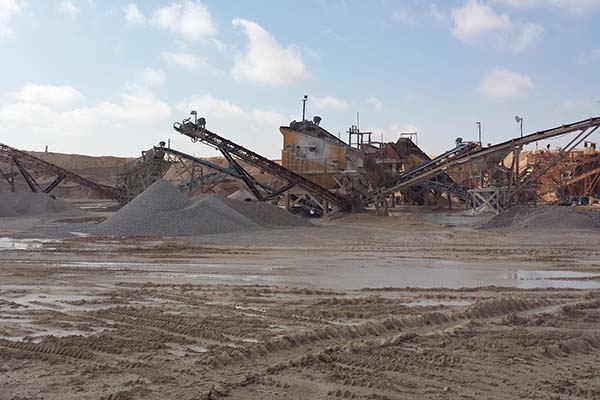
Their project is located in Suman, which is to crush limestone from 500mm into 3mm, 3/16”, 3/8”, 3/4” at 100tons per hour for road and building construction.
For the limestone is not so hard, whose Mohs’ Hardness Scale is about 2-3, usually we use impact crusher as secondary crusher to process it. The life-span of hammers and liners are longer. What’s better, the shape of final outputs is cubic, which is better used in building and road construction.
The impact crusher not only perform multi chamber crushing and improve equipment efficiency, but also specially treated parts such as plate hammers have good wear resistance and extremely low wear rate. Not only is the particle size fine, the particle type regular, there are few needle-shape materials, and the grading is very high.
The impact crusher can effectively handle materials with high moisture content and prevent blockage of the crusher. When dealing with materials with excessive moisture content, the feeding chute and impact plate of the impact crusher can be equipped with heating devices to prevent material adhesion. The impact crusher does not need to be equipped with a bottom sieve plate to effectively prevent blockage.
When non crushing materials (such as iron blocks) enter the crushing chamber, the front and rear impact frames retreat, and the non crushing materials are discharged from the machine; When the crusher resumes operation, the impact frame automatically returns to its normal working position with the help of a self weight safety device, thereby avoiding the risk of equipment overload and losses caused by shutdown maintenance. Due to the automation of the entire process, it greatly reduces manual downtime for cleaning and maintenance, greatly improving the production efficiency of the entire production line.
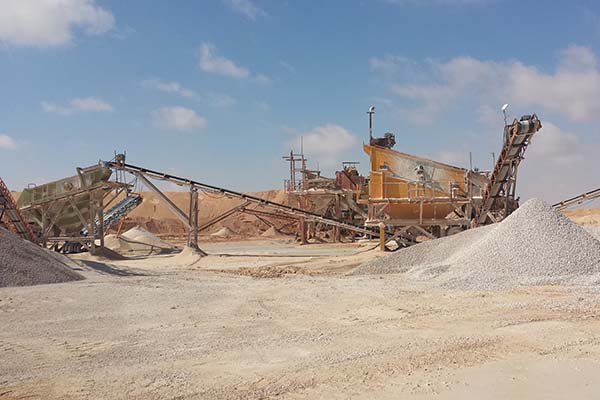
If you want to visit this project on site, or contact our client to check the machine’s work performance, please contact us: WhatsApp:+8613838097071